Configure the protections and profiler parameters according to your motor's needs. Open the Sensorless wizard.
The order of the steps to tune the motor in sensorless mode is shown in the next picture.
First of all, tune the torque loop using the TORQUE tab. To do this, the torque actual should follow the torque demand as closely as possible. The torque tuning will start once the enable button is pressed, and it can be configured with the two sliders for proportional and integral constants. More options can be selected when clicking on the "Basic/Pro" button.
Start-up configuration
After the torque is correctly tuned, the start-up ramp needs to be configured. The start-up procedure consists of a time slot where the motor is locked to a known position and a velocity ramp in open-loop mode. This window will perform the configured start-up ramp and will repeat the process until the final configuration is achieved. To perform the start-up configuration, the user needs to be able to have visual contact with the motor. Note that the parameters for start-up depend on the motor and the load that it's carrying.
To perform the start-up configuration, the user needs to be able to have visual contact with the motor. Note that the parameters for start-up depend on the motor and the load that it's carrying.
To configure the start-up:
By clicking on the "Basic / Pro" button, the lock stage can also be configured. The configuration set here will affect how fast the motor starts-up and how well the ramp is performed.
In the Start-up window, the velocity reading of the drive will be plotted. If nothing is plotted, the reason could be that the Observer gain is too close to 0. This has to be changed in the "Observer" tab
Since the process is repeated several times, the user can check the effect of the changes in the start-up process. To start this process, click on "Enable".
Observer configuration
Once the motor can keep up in open loop, the observer is tuned. To do this, the motor will run in an open loop and the estimated and measured currents alpha and beta will be plotted. Two parameters are used to tune the observer:
- Gain: Defines the amount of correction that will be applied to the motor's virtual model in each iteration of the algorithm. This is what allows the current estimation to slide along the measured currents.
- Linear zone: Defines a region of current error (Estimated current - Measured current) in which the gain will be applied proportionally to the error in that time instant. If the error is out of the linear zone boundaries, the gain applied will be the saturation value defined in the Gain parameter.
To start tuning these parameters click on "Enable".
The tuning of these parameters is visual. The estimated current's switching ripple should stay between 10% to 30% of the measured current's peak to peak value. Too much ripple might cause angle imprecision and chatter at higher speeds, and low switching ripple might cause the estimator to not correct the model fast enough.
Once this is correctly tuned, the velocity tuning needs to be performed.
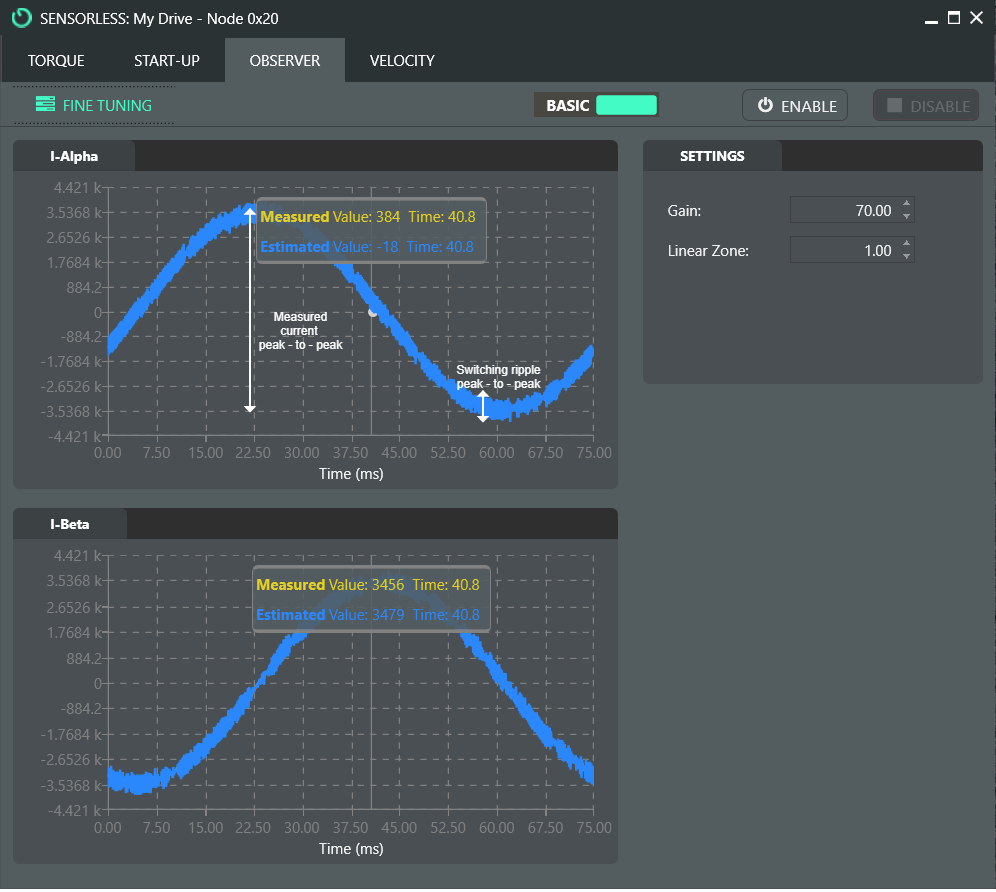
Velocity tuning
To tune the velocity, click on the velocity tab and press "Enable". The drive will try to start-up the motor. Initially, there will be no velocity tuning so the motor will not close the loop correctly. As the drive will detect a motor stall, the start-up will run again.
In order to close the loop increase gradually the "Velocity Proportional Constant" (Kp) using the slider highlighted in the next picture. When this value is in a good range, the loop will be closed and the velocity will increase following the profiler's acceleration ramps. If necessary, the Velocity Integral Constant" can also be increased using the Ki slider. Additionally, the integral limit can also be modified by clicking on the "Basic / Pro" button.
Excessive gains can cause unstable behavior in the system.