How to configure a rotatory brushless motor with SSI encoder feedback
Problem
I have a rotatory brushless motor with an SSI encoder as the only feedback but I don't know how to properly configure it and tune it. What is the right process that I need to follow?
Clarifications and checkings
- This article describes (step by step) the manual process of configuring a rotatory brushless motor with SSI encoder feedback with very optimal performance. A more automatic way of doing this configuration could be by using the Configuration Wizard with all the implications that this might have.
- This step by step process assumes that your motor does not have a brake. If you do have one, ensure that you have configured it correctly like it is shown in the following article before proceeding with any configuration: How to configure the brake of your motor.
- This step by step process assumes that neither the motor or the power stage of the drive is damaged. Please, if you are not sure of this, follow the instructions in the How to know if the motor phases or the power stage of the drive are damaged article in order to verify it.
- This step by step process assumes that your feedback device is working properly and no noise is coupled to the SSI encoder lines. Please ensure that you have checked this by following the step process described in How to know if the feedback device is working properly.
- This step by step process assumes that the SSI encoder is not mounted on the output shaft of a gearbox that is placed after the motor. The SSI encoder needs to be on the shaft of the motor or the commutation will be done erratically.
- This step by step process assumes that there is no digital input mapped to the "Motor Enable" functionality of the drive. If that is the case, ensure to have the digital input ON (if active high, otherwise OFF) in all the steps that involve movement during the configuration or otherwise those steps will fail.
Steps
- First of all, if you don't know already, you need to know that there exists a special firmware version designed for applications with SSI encoder as the only feedback device. When you update the firmware of your drive automatically you will be updating it with the standard version, therefore you need to do the update manually in order to use the "SSI only version". You can find this firmware versions from 2.6.1 version and on, and you can download the firmware files directly from the Downloads page. In both EtherCAT and CANopen versions, you will find both "Standard" and "SSI only" versions of the firmware:
- Once you have connected to the drive, go to the Actuator window and set the right parameters for the Motor Type, Position sensor and Velocity sensor. Your window should look like the following:
- Then, you need to go to the Motor window in order to input all the motor data from its datasheet (it should all be in there). The parameters that you need to input mandatory are torque constant, continuous current, peak current (if known), max permissible speed and motor pair poles. The inductance and the resistance can be obtained in later steps with the system identification included in the torque tuning stage and the rated torque can be determined by the product of torque constant and continuous current. An example of motor parameters for a brushless motor could be the following:
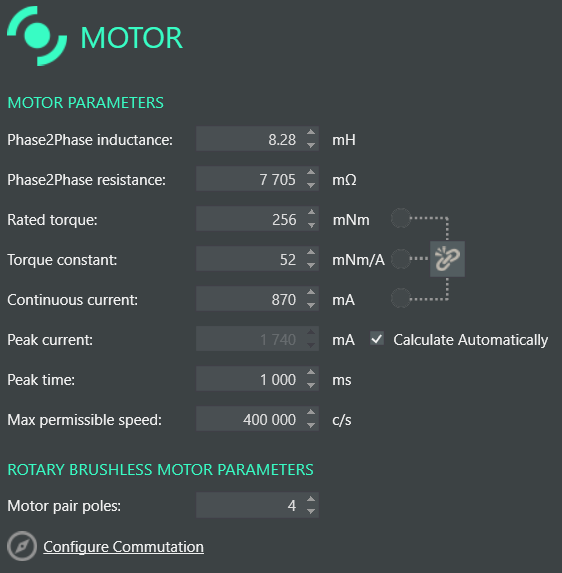
- Then, we need to input the parameters of the SSI encoder that we will encounter from the datasheet in the SSI Absolute Encoder window. We will need to input all the parameters besides the Polarity, which needs to be determined by following the procedure that is explained in this article: How to calibrate the polarity of your feedback device manually. If you are not familiar with all these parameters, here is an example of the frame of an SSI encoder and how all these parameters can be extracted (besides the Polarity obviously):
- For such encoder, the parameters would be:
- Type: 3 status bits at the end of the frame
- Size: 27
- Codification: specified in the datasheet
- Max. clock rate: specified in the datasheet
- Single-turn bits: 14
- Single-turn start bit: 3
- Multi-turn bits: 9
- Multi-turn start bit: 18
- Endianness: MSB
- The following picture shows an example of a configuration of an SSI encoder:
- After having configured the Polarity correctly, it is time to move to the Commutation window in order to calibrate the initial angle of the motor. Because of its absolute nature, we can use the SSI encoder as both Commutation sensor and Reference sensor and "Non incremental sensor used" as Initial angle determination Method like it is shown in the following picture. Then, we only need to use the Calibrate tool to calibrate the initial angle. Start by using a small amount of torque and keep increasing it until you get enough movement to get the test finished successfully:
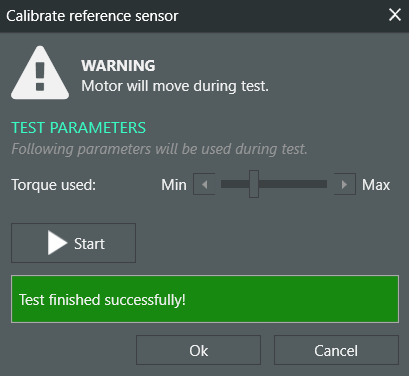
- After having successfully calibrated the reference sensor, it is of good practice to do a quick verification to ensure that the commutation has indeed been properly calibrated. This can be very easily done by using the Open-loop by using the commutation sensor mode from the Move window while plotting in the Scope both position and velocity actual values. Try applying different target voltages in both directions and check that the motor is spinning at the same speed (for a certain target level) in both directions. If the motor does not spin the same way in both directions, if it spins erratically in one direction or any other strange anomaly please repeat the previous step and recalibrate the initial commutation angle. An example of this verification procedure is shown in the following image.
- Once the calibration is verified, it is time to move to the Limits window. In that window, make sure that your position, velocity and torque limits are properly set accordingly to your system. Make sure that the position limits match your motion range (if there is one), that the velocity/acceleration limits are correct and that the minimum and maximum torque limits match the peak torque value:
- After having set the Limits correctly, make sure that the Protections parameters are set up correctly as well. Adjust the voltage range to your application's and make sure that the maximum system current is equal to or higher than the peak current value:
- After this last step, the configuration is ready to start with the tuning of the different motion loops. In order to do a proper tuning, we advise to take a look at the following links:
SmallBestOriginalRemove